Automated coating application
Paint, gelcoat, and fiberglass
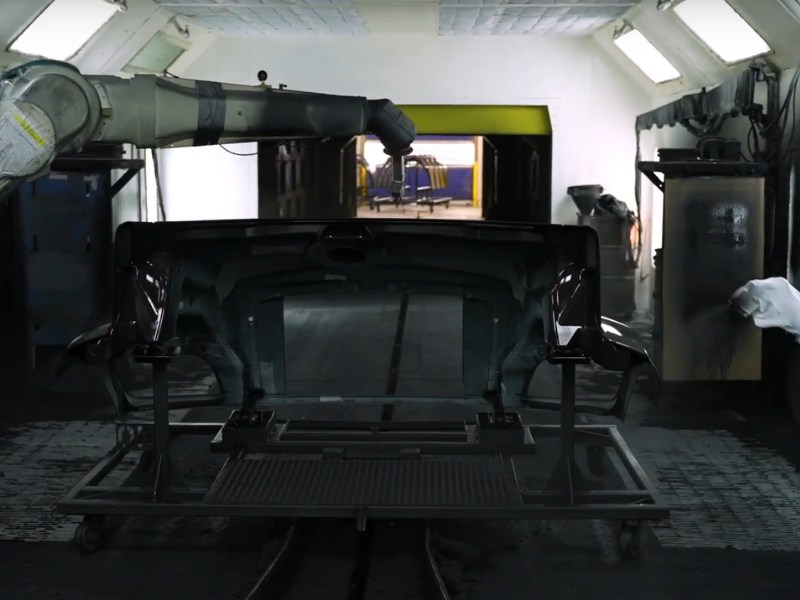
Key Benefits
Increased Productivity:
Unlike manual operations prone to breaks and interruptions, robots maintain consistent performance, ensuring uninterrupted production and optimal equipment utilization.
Raw Material Savings:
The precision control exercised by robots ensures a uniform finish quality while optimizing raw material usage. This efficiency leads to significant savings, as every quantity of paint is used in the most effective way possible.
Reduced Rejection Rates:
By maintaining consistent quality, robots lower rejection rates, resulting in substantial savings by avoiding rework or reprocessing of defective parts.
Frequently asked questions
If we look at the serial robots currently available on the market, we could say that virtually all of them have the functionality to move around and perform painting tasks. However, painting robots are generally a little different. In many cases, paint application requires explosion-proof equipment. So most painting robots are certified to meet this requirement. They also have other features useful for paint applications, such as long reach, a hollow wrist for hose management, different geometries to facilitate access to parts in certain applications, and software options to facilitate integration/programming.
At Revtech Systems, we specialize in the integration of several different robot brands, including ABB, Fanuc, and Yaskawa robots. We also integrate Cartesian painting robots, which can be either 1-axis or 2-axis reciprocators for painting parts with relatively flat geometries. How to choose the right brand? ABB, Fanuc, and Yaskawa all have excellent products, so, unfortunately, the choice is not so obvious. Depending on the details of your project and installation, one brand may stand out over another. Contact our team to discuss and make the right selection for your painting robotization project.
No. Serial robots such as those used by manufacturers like ABB, Fanuc, and Yaskawa have many advantages, especially when application trajectories require a lot of orientation changes. When producing parts with flat geometries that require little variation, we integrate Cartesian/Linear (Gantry) robots with one or two axes of movement.
For painting large parts, whose dimensions exceed the working envelope of a robot, there are various options open to you. However, the first step is to work with our team to run a simulation in order to test several different robot positions. Alternatively, the first option is to use an overhead or floor conveyor to move the part in front of the robot. The robot follows the advancement of the part and applies the paint in coordination with it. The second option is to position the robot on a linear axis (rail). This creates a 7th axis for the robot, and allows relative movement between the part and the robot, to maximize robot utilization.
In a context of labor scarcity, it's easy to say that part of the return on investment of a robotized paint cell is the savings on labor costs and social charges. But it's not the only point to consider and it's often not where the majority of $ is. The consistency that the robot brings to our production in this kind of application is really the key to return on investment. Consistency will bring gains in productivity, unlike the manual process which fluctuates greatly over a shift (break, lunch, wash-up, etc.). Consistency of process control by the robot will bring considerable savings in raw materials since the quality of the paint application can be consistently achieved using a minimum of raw materials. And finally, consistency will bring considerable savings in quality control and reduced reject rates.
This question can be broken down into different stages or aspects. The simplest solution to robotize painting remains low mix/high volume production, i.e. mass production where we have large batches of the same part. In this case, robotization is simple and effective. It's a 'no brainer'. The second phase is to see if we can isolate families of parts between which certain variables, mainly dimensional, can be used to adjust painting trajectories in real-time. The final phase consists in ensuring that no two identical parts follow each other on the production line. This is the most complex process to integrate in terms of robotization. With Revtech's experience in all levels of paint robotization, we recommend that you contact us to discuss the best robotization strategy for your production.
The use of a vision system in an automated painting cell is particularly useful in the case of high mix or dimensional changes in parts of the same family. It's important to understand from the outset that it's vital to define your needs and choose the right vision system for your robotization project. The first step is to define what needs to be identified as a variable on the line (geometry, dimensions, position, part recognition, etc.). Then look at what systems are available, starting with the simplest possible solution. Don't overlook RFID and barcode solutions for part identification before considering 1D, 2D and 3D vision systems.