Automated welding
Welding robot
At Revtech Systems, we revolutionize your welding processes with advanced robotic solutions tailored to your unique needs. Whether you choose collaborative robots (cobots) or industrial robots integrated into custom robotic cells, we provide cutting-edge technologies designed to maximize productivity and deliver optimal weld quality.
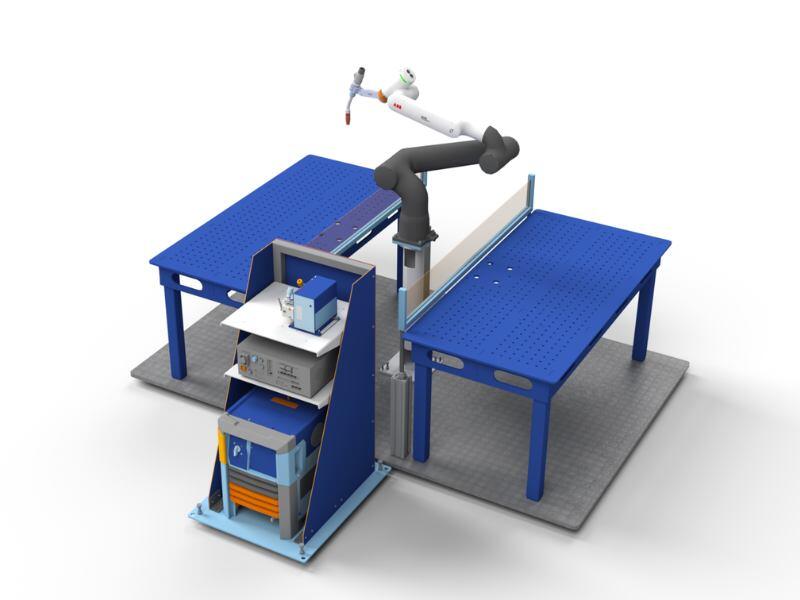
Simplified Programming with the Easy Teach Device
With GoFa’s Easy Teach device and ABB’s Wizard Easy Programming graphical tool, you can program your welding paths in under 2 minutes—effortlessly. Watch the demo video!
Revtech Systems is proud to be the very first ABB-certified Service Value Provider robotic integrator in Canada, ensuring the best support for your needs.
The Revtech Difference: Comprehensive Support
Our commitment goes beyond delivering a robotic cell. We understand that implementing and effectively using a robotic welder in your facility can be challenging. That’s why we put support at the heart of our approach.
At Revtech, we ensure that your equipment operates at its full potential. Our experts guide you every step of the way—from assessing your needs to training your teams, programming, and maintaining your systems. This personalized support guarantees successful integration and long-lasting optimization of your processes.
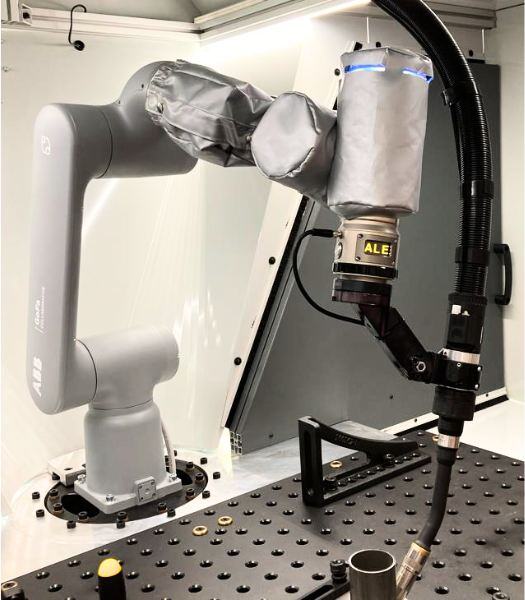
Collaborative Robot Welding Cell
The Collaborative Robot Arc Welding Solution makes creating and executing welding sequences significantly easier. Its main innovation, the Easy Teach Device, uses lead-through programming and interactive buttons to precisely define weld points.
With the ongoing shortage of experienced welders, businesses need user-friendly automation solutions to stay competitive. This solution was designed to reduce the complexity of robotic welding, making automation more accessible—especially for SMEs and beginner welders.
Why Choose a Collaborative Robot?
- Flexible solution for low-volume, high-mix tasks
- Helps train and upskill workers
- Automates repetitive tasks for greater consistency
- Suitable for users with varying programming experience
- Reduces deployment and redeployment time
- Delivers better quality and less waste compared to traditional welding
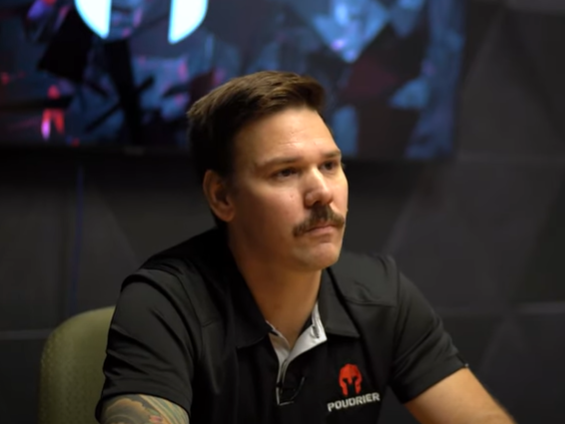
Customer Testimonial
"Revtech Systems worked with us in a very collaborative way. I would definitely recommend Revtech to any company looking to adopt a welding cobot. It was a straightforward and truly rewarding experience."
- Vincent Lobry, Welding Team Lead, Poudrier
Evaluate your project
We understand that every business is unique, so we'll work closely with you to understand your specific needs and design customized automation solutions. Our team of experts in robotics, artificial vision and AI is here to guide you every step of the way on your next automation project.
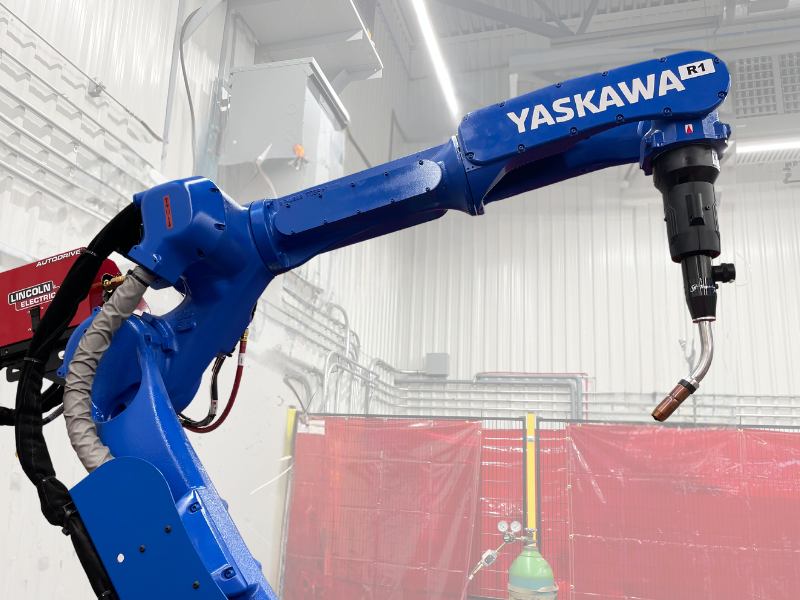
Frequently asked questions
Integrating a robotic welding solution into your existing welding cell requires several steps. First, make sure you've purchased the right robotic welding solution for your application. Next, you'll need to reconfigure the space in your welding cell to accommodate the robot. This reconfiguration may include modifying the layout of the workshop and adding specific equipment for the robot.
In addition to space reconfiguration, the integration of a welding robot may require the addition of equipment such as safety devices, vision systems, special work tables, and cable management devices.
Some customized industrial cells do not correspond to standard cell specifications. They are equipped with additional axes and parametric programming to automatically adapt the robot and fixture to specific applications.