CNC machine loading (Machine tending)
REVFLEX PROMOTION
CAD$10,000 discount
Take advantage of a CAD$10,000 discount on our Revflex solution if you place your order before May 15, 2024.
What our solution includes:
Revflex base with easily customizable cart for your parts loading system
- UR10e robot including connectivity/machine integration box and touch-sensitive programming terminal
- Hand-e robotic gripper for gripping flexibility
- 4.0 productivity monitoring module
- 3-day training at Revtech for 2 people
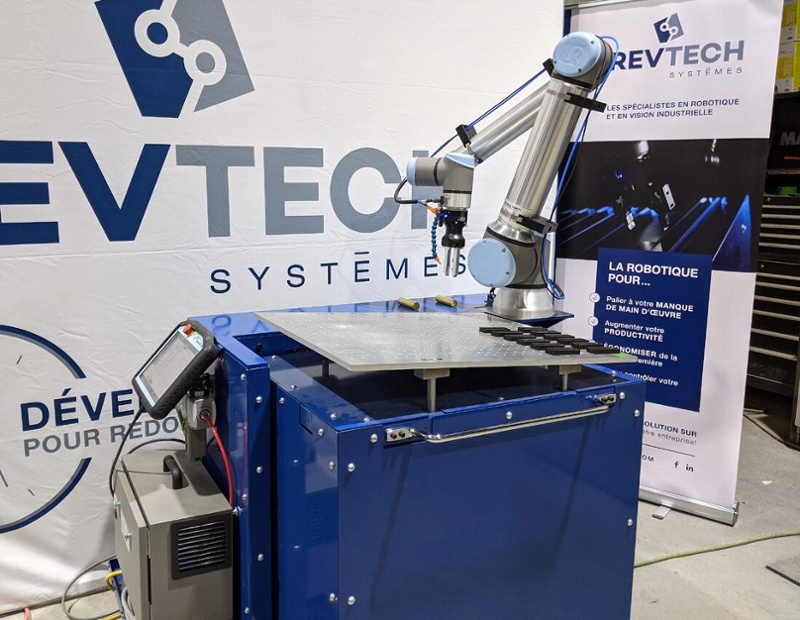
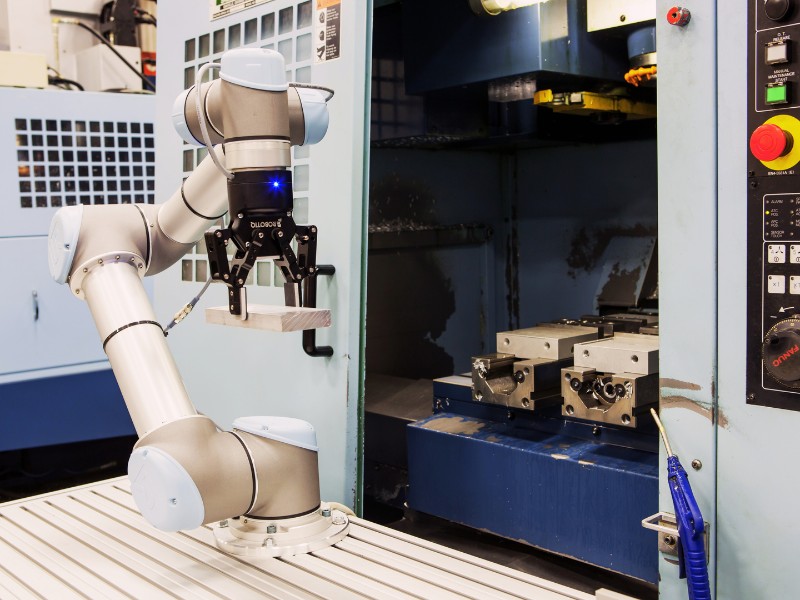
A simple solution
Free Yourself from Tedious Tasks with Our CNC Machine Tending Service You don’t need technical expertise to benefit from automation. Simply integrate a collaborative or industrial robot into your CNC machines and presses to boost productivity and enhance your team’s skill set.
THE REVFLEX SOLUTION
A simple solution helps you quickly become autonomous with technology and accelerates ROI.
Station
- Moveable and relocatable station.
- 4.0 connectivity and machine integration box.
- 4.0 productivity monitoring module.
- Easily customizable cart.
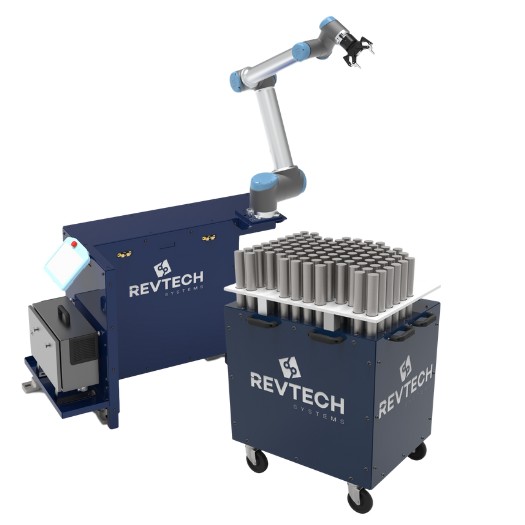
CMM solution
In addition to loading and unloading your CNC machine, this solution enables the robot to perform part quality inspection using a CMM, a significant improvement over conventional CNC loading methods.
This allows immediate quality control after part machining, facilitating automatic correction of the next machining run, or immediate pausing of production to avoid rejects.
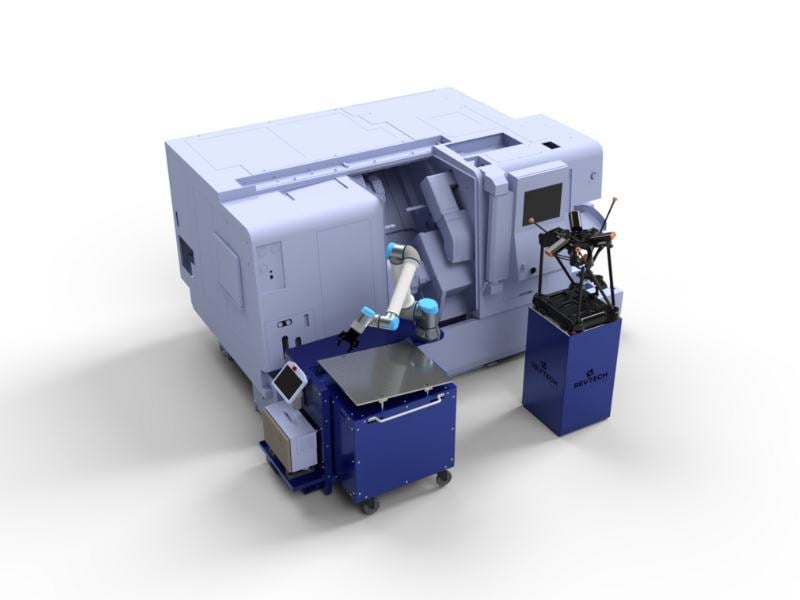

Our collaborative robots specialize in loading CNC machines.
.jpg)
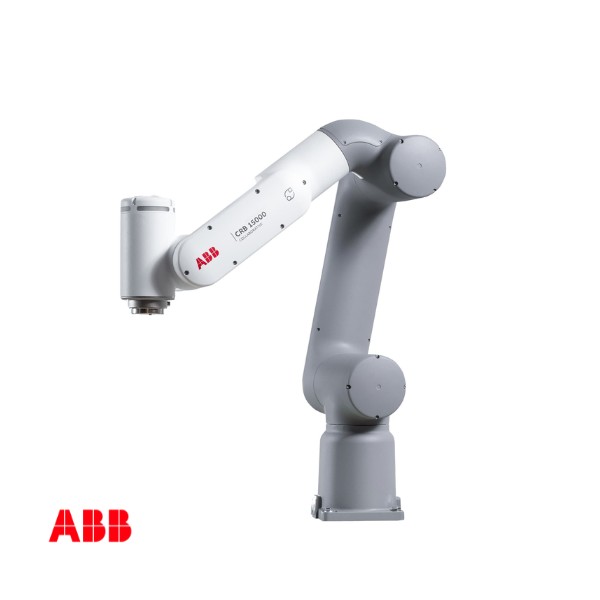
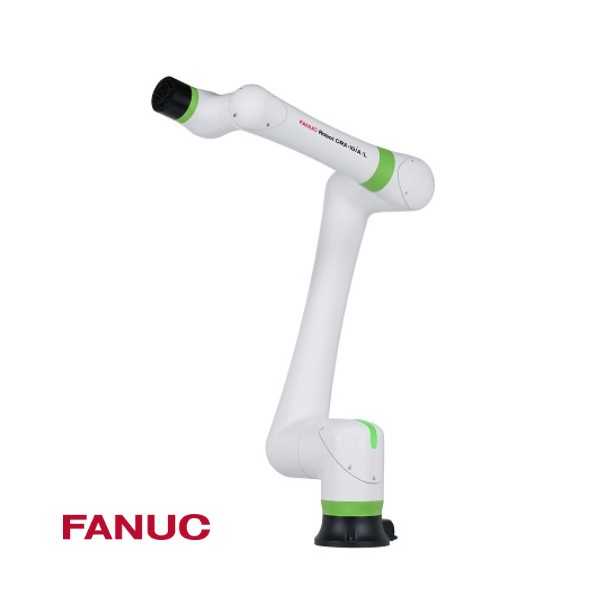
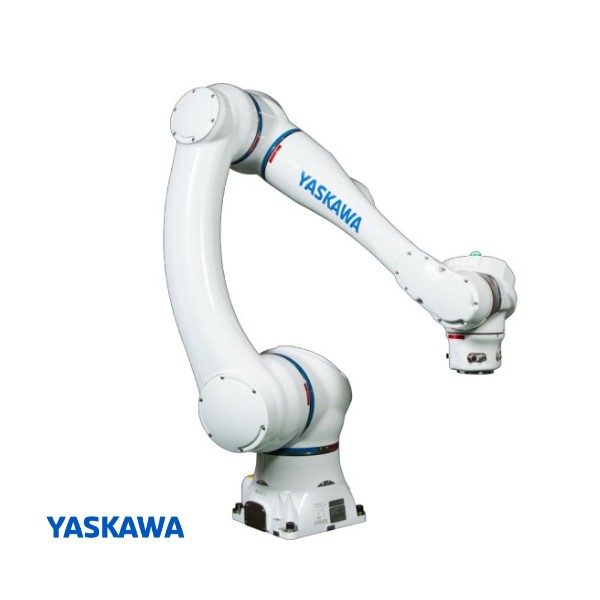
Comprehensive Training Included
2 Days of Certified UR Robot Training Included Gain full autonomy with your station.
ROI in Less Than 2 Years!
With 2 Work Shifts. Maximize your current CNC machines' output and eliminate downtime.
50% Less Programming
URCap Software for the Station. Pre-programmed part handling included.
Frequently asked questions
A robot can easily be installed on different CNC machines (lathes, milling machines, bending machines, grinding machines, etc.). Nor is there any real limit to the brands of machines the robot can be integrated with. It is, therefore, possible to integrate a robot into machines from Mazak, Haas, Fanuc, DMG Mori, Amada, Trumpf, Nakamura-Tome, and more.
The first answer to this question is not to ask yourself this question from the outset when you're looking to automate the loading of your CNC machine. Both technologies are applicable to this kind of application. Start by looking at the format of your parts (geometry and, above all, weight). Then look at the range required for your application. This means looking at the distance inside the machine for part loading, and how the parts will be fed. Then look at your machining time (spindle time) to quantify the real gain of having a higher speed with the industrial robot than with the cobot. And finally, think about the variability of your production, how everything will be programmed, and who will be in charge of operating, improving, and programming your robot. With these answers, you'll be able to make a better decision about which robot technology, collaborative or industrial, is best suited to your application.
Yes, it's possible to deploy a robot cost-effectively in a low-volume application. With Revtech's flexible solutions, it's possible to start up a new part in 10 minutes at the robot programming level. You can then analyze the machining time (spindle time) and the quantity to be produced to see the benefits of using a robot for your production. You can also consider our mobile collaborative robot solution, which will enable the robot to move autonomously between machines and load several low or high-volume productions.
Yes, it's possible. In fact, one of the key advantages of using a collaborative robot for CNC machine loading is its ease of use on multiple CNC machines. Revtech has several solutions for this. The first is the manual changeover of the robot between machines. Depending on the positioning of the machines in the factory, it may be possible to position the machines so that the robot can access more than one machine. If the machines are relatively far apart, a solution with a linear axis can increase the robot's reach, enabling it to load more than one machine. Finally, the most flexible solution is our mobile cobot solution. In this solution, a collaborative robot mounted on a mobile robot navigates autonomously between machines in the plant, to load them. Contact our application experts to discuss the various possible solutions.
Of course, labor savings is the first aspect of ROI that comes to mind. But there are other variables to consider. The use of a robot enables more punctual machine loading. In other words, as soon as it's ready for loading, the robot carries out the task, whereas, with an operator, we can't guarantee that he'll be immediately in front of the machine for the task. There will also be a gain in production during breaks and hours when no human is present in the plant. Meanwhile, the robot continues to feed the CNC machine. It is also important to consider what the human who has been freed from this task will do instead. There will generally be a quantifiable gain in productivity.
Yes, there are several ways of performing quality control with the robot cell. Quality control can be carried out by loading into a CMM, by inspection with an artificial vision system, or by adding a dedicated metrology station. In addition to quality inspection, other tasks such as cleaning and deburring can also be added in masked machining time. The choice of what can be done is generally linked to the machining time of the part, which gives us the range of masked time in which the robot can perform other tasks.