Material Dispensing
Automation project with a FAST return on investment!
Whether it is to apply glue, sealant or other types of adhesives, Revtech Systems is the reference, with its experience in this field. Indeed, thanks to the precision and the repeatability of robots, some of our customers managed reduce their use of adhesive by almost 30%, in addition to solving lack of labor and quality issues! The return on investment of an automated material distribution project is among the fastest of the various possible robotization projects!
.jpg)
Key Benefits
Labor Cost Reduction:
Robots work continuously, without breaks or benefits, reducing payroll expenses.
Increased Productivity:
The constant operation of robots boosts production speed and output.
Loss Reduction:
Robotic precision minimizes defective parts and lowers non-compliance costs.
Floor Space Savings:
Compact and easy to integrate, robots reduce the need for additional workspace.
Raw Material Savings:
Robots apply the exact amount of material needed, minimizing waste and maximizing savings.
Which Robot Should You Choose for Your Application?
To determine the most suitable type of robot for a given application, it’s essential to consider the specific needs of the task. For example, if the application involves simply applying adhesive to a flat, non-tilted surface using a dispensing gun, a Cartesian robot — also known as a gantry robot (which moves linearly along the X, Y, and Z axes) — might be an appropriate choice.
If the application requires the gun to tilt and follow a 3D trajectory, as shown in the video, a 6-axis robot will be necessary. The choice between a collaborative robot and an industrial robot depends on several factors, including the desired production rate, the ease with which trained operators can modify trajectories, the proximity of the robot to human workers, and safety considerations.
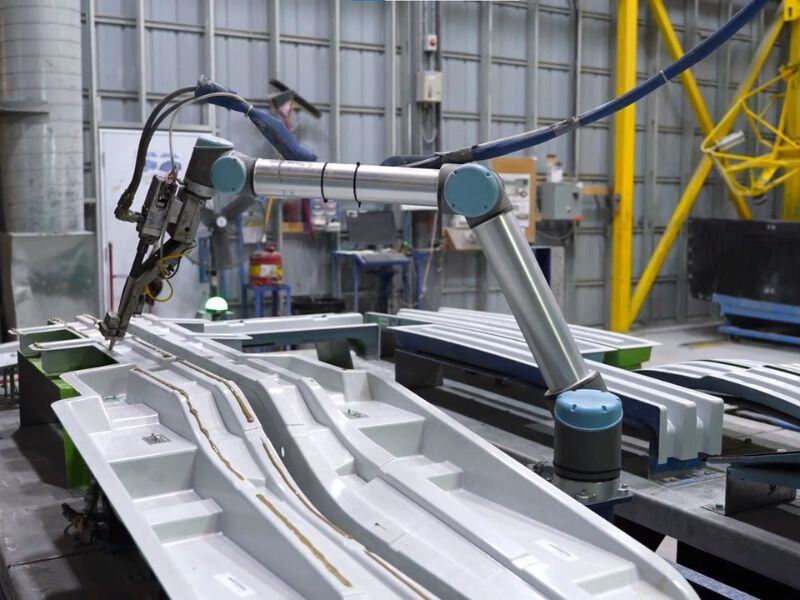
Frequently Asked Questions
For an Automated Material Distribution project, almost any type of robot can be used. Indeed, it is the application that will define the type of robot that can be used. Let's assume, for example, that we only need to apply glue on a flat, non-sloping surface with the glue application gun. In such a situation, it will be possible to consider the use of a Cartesian robot (i.e.: a gantry, a machine that moves in X, Y, and Z translations only). On the other hand, if the application requires that the gun tilts to follow a 3D trajectory, as it can be seen in the video at the top of this page, then it will be necessary to use a 6-axis robot . The choice between collaborative and industrial robots is based on: 1) the desired production rate, 2) the ease with which trained operators can modify the trajectories, 3) whether the operators need to work in close proximty to the robot, and of course, 4) a safety analysis.
YES ! It is quite possible to automate even in a "High-mix / Low-volume" situation. The first thing to look at in such a situation is the possibility of creating product families. Indeed, between a rectangular product that measures 10 cm by 10 cm and another that measures 40 cm by 40 cm, only one or two parameters need to be changed. In the case of a more drastic geometric variation, it will be necessary to consider whether to integrate measurement sensors, 2D vision or 3D vision.
Good question ! Indeed, many of our clients ask this question. Our answer is...almost everything. To summarize, the robot moves the application gun. So, if an operator is applying a certain product from a certain application gun, it's hard to imagine what would prevent a robot from performing the same task. The key aspects are generally the reach, the maximum payload of the robot as well as the method of controlling the flow rates of the applied material.
The return on investment of an automated cell is a concept that any good project manager must master. Indeed, it is the conlusions from a financial analysis that will justify moving forward with an automation project. In the case of Automated Material Distribution, it is necessary to consider the following elements: operator salary, social benefits, potential increases in production, savings in relation to defective parts, savings in floor space AND ESPECIALLY raw material savings. Indeed, this saving is mainly justified by the fact that a robot is always constant in its movements, which makes it possible to apply the minimum required glue and know that it will always meet quality control requirements.
QUESTION
Can I use the same material distribution equipment that I currently have (pump, gun, etc.)?
99.99% of the times a customer asks us this question, the answer is...yes! Indeed, if your equipment allows complete autonomy (access to a product tank) or partial autonomy (change cartridges a few times a day), and if it is possible to control the On/Off of the flow rate electrically or pneumatically, it is possible to install your equipment directly on the robot. Our in-house specialists will share their expertise with you, so that everything is easily installed!